Strakes openings placement (1.0 hr)
For the first time since I started putting bulkheads and sidewalls together, the fuselage has left the table and is now on sawhorses, holding itself together at last.
Still upside down on sawhorses |
The next step at this point would be to put the bottom foam on the fuselage (top in the previous picture), and trace the outline of the floor onto the foam, from the inside. The only problem is that when I made my initial purchase, I never did order the foam for the bottom.
Doh!
A quick call to Wicks, and the foam was in the mail, but now I'd have to wait another week to get the stuff.
Perfect time for some more glamour shots, after turning the fuselage right side up!
Right side up for the first time |
Flintstones' car (note my legs sticking out of the bottom) |
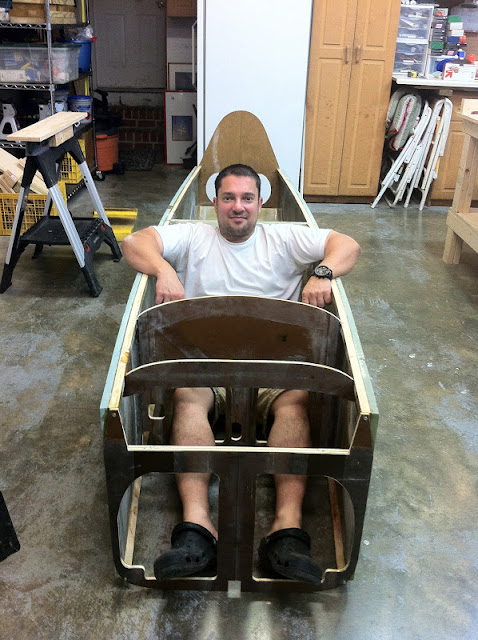
![]() |
Look at the difference 2" make. The longerons are buried into my shoulders in the per-plans rear seat on the right. |
With nothing on the agenda, I decided to trace the holes for the strake access on the fuselage sides. That will help me position the peel-ply when I later glass the exterior of the fuselage.
Rear seat, strake access hole |
Front and rear seat hole patterns |
One of the plan changes I decided to incorporate in my plane, is what I have called the "Steve's elbow mod" in the past. Essentially it creates more elbow room for the rear passenger, by extending the trailing edge of the rear strake access hole further back.
In my case the strake cutout begins 13" (33 cm) from the front side of the firewall, compared to the original 21.5" (54.6 cm).